Low carbon bricks for your project as disruptors tackle climate change
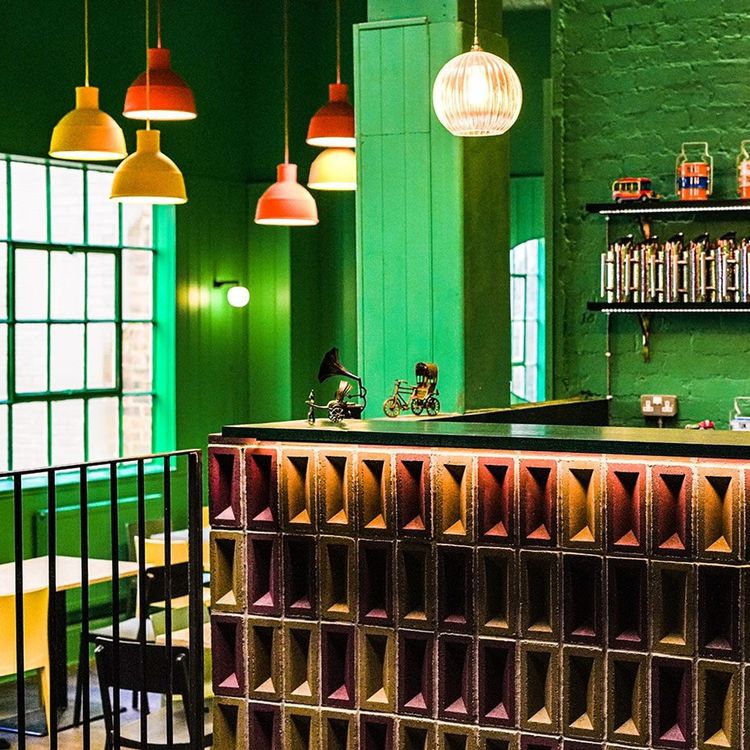
Is it possible for a new generation of bricks that use recycled waste, do not require cement, and do not need kiln curing to reduce the environmental impact of the industry?
Bricks have a rich history and continue to be the dominant choice for constructing buildings in the UK. In 2019, a staggering number of approximately 2.6 billion bricks were manufactured in the country.
However, our insatiable desire for this long-lasting, tangible, and frequently attractive item depletes vast quantities of energy, emitting greenhouse gases and other detrimental contaminants into the air.
Baking clay bricks at temperatures exceeding 1000ºC using kilns powered by fossil fuels is quite demanding in terms of energy consumption. Clay, which is a limited resource that occurs naturally, needs to be extracted and transported across the world, which also leads to the creation of process emissions that are challenging to minimize.
The brick making sector is making efforts to tackle its impact on the environment. It has initiated a roadmap for decarbonization and energy efficiency, which has provided funding for projects aimed at reducing energy consumption and emissions. Additionally, there are future plans to invest in efficiency and renewable energy sources. For instance, Forterra's new Desford plant utilizes low-carbon fuels such as hydrogen (similar to Michelmersh's HyBrick) and adopts electric-firing. According to the Brick Development Association's report in 2022, there has been an 8kg CO2e/m2 reduction in emissions since 2015. The industry average for clay bricks stands at 26 kg CO2e/m2, compared to the average of 27.3 kg CO2e/m2 for traditional clay-fired bricks (as per the EPD 2019-2024 Brick Development Association).
Nevertheless, as the demand for bricks continues to rise, the UK's dependence on imports from Europe and other regions is also increasing. The government has set a target of constructing 300,000 homes annually by 2025. To ensure that the national net zero carbon goals for 2050 remain attainable, a series of ambitious steps will be necessary.
Taking on the task with determination, brick producers and scientists are leading the way in developing brick options with reduced carbon emissions. These innovative alternatives involve utilizing methods that consume less energy and follow circular practices. For instance, recycling demolition waste, using curing processes that do not require kilns, and employing binders that do not rely on cement. In addition to establishing new brick factories, various construction projects are currently being implemented to test these environmentally-friendly approaches.
Carbon footprint: Approximate 1.006 kg of carbon dioxide equivalent per square meter (A1-A3). Anticipated period until product launch: Prospected BBA certification in the United Kingdom can be concluded by September 2023.
With a carbon footprint that is less than 5% of a typical clay-fired brick, K-Briq stands out for its minimal energy impact. Additionally, it boasts the highest proportion of recycled materials in any brick available, with construction and demolition waste making up 90% of its composition.
K-Briqs have the potential to serve as an alternative to conventional clay or concrete bricks for many exterior or facing brick uses. These innovative bricks possess similar strength as their counterparts and an array of additional advantages including increased thermal mass, lighter weight, and are available in an extensive range of 13 stock colors.
The item is not baked and the relatively limited amount of water in the mixture, together with the utilization of an exclusive binder that does not contain cement, enables it to solidify in less than 24 hours. Verification of "end-of-waste" label by the Environment Agency confirms that it is devoid of harmful substances and can be entirely recycled.
The company is presently collaborating with two contractors who specialize in managing construction and demolition waste. According to Lucy Black, the head of business development at Kenoteq, it is of utmost importance to team up with waste management partners who hold proper certification and can offer waste streams that align with regulations, while maintaining the desired quality and granular density.
Kenoteq's facility in Scotland has the capability to produce 5 million bricks annually. In 2024, they will be implementing a range of projects for early adopters. These projects will consist of a highly efficient retrofit for a housing association that achieves net-zero energy consumption, a significant undertaking for a local authority, and the construction of a welcome center for an influential developer. Additionally, Kenoteq will also be engaged in smaller projects involving extensions and interior renovations.
Utilizing a region-specific strategy for obtaining waste materials and distributing products, Kenoteq intends to expand production to various locations across the globe.
Black explains that they will promptly set up agreements with other waste contractors and distributors to expand their business. They anticipate having around six to eight factories in the UK within the next five to six years. Furthermore, they have been granted patents in the US and Europe, with one still pending in Canada. As a result, their international efforts will initially center around these countries.
CO2 emissions related to production: 17 kilograms of CO2 equivalent per square meter (from the beginning of production to delivery, based on the latest EPD certifications for 100mm cavity masonry blocks). Ready for purchase without any waiting time.
Porotherm presents a slight decrease in carbon footprint when compared to conventional clay bricks. It is potentially more appealing as an alternative to concrete blocks, as the 100mm cavity masonry blocks manage to reduce around 40% of embodied carbon in comparison to their concrete counterparts.
Morgan Sindall claims that by using Porotherm blocks instead of the customary cement blockwork during the construction of the Addenbrooke Care Home in Gosport, Hampshire, they were able to reduce the associated carbon emissions by an impressive 324.5 tonnes.
The thin-joint system has become a popular choice for residential buildings in Europe. It is available in various sizes to accommodate inner leaves or rendered outer leaves of cavity walls, single leaf external walls without joints, infill panels within framed structures, and both load bearing and non-load bearing partition walls.
According to Andy Oram, who oversees the Porotherm project at EH Smith Builders Merchants, a distributor in the UK, the firing process for these blocks can be carried out at lower kiln temperatures. Oram states, "Firing is an unavoidable disadvantage when working with clay products, but Porotherm is fired at a reduced temperature of 985º Celsius, which is considerably lower compared to the range of 1100 to 1500ºC required for traditional bricks."
The modules are punctured and include 30% of resources sourced from alternative, recycled, or secondary origins, thus diminishing the necessity for fresh clay. The modules interlock with one another, resulting in a decreased requirement for mortar to secure them, subsequently reducing water consumption during construction by 95%.
According to Oram, removing a vast quantity of water during the manufacturing and installation process brings about advantageous effects on the construction technique. This eliminates the need to utilize electric-powered heaters and dehumidifiers to dry the wall before adding the plaster finish.
The frequently utilized 365mm solid block is primarily employed in the United Kingdom and produces approximately 47 kg/m² of carbon. However, according to Oram, this essentially serves as your complete wall, eliminating the necessity of brick, cavity insulation, and concrete blocks. Oram concludes that all you need to do is apply the finishing touches to both the interior and exterior.
Amount of carbon dioxide emitted during production: 26.25 kilograms per square meter, according to EN15804+A2:2019. Time needed for product to reach the market: One occasion.
To provide an understanding of the challenge involved in creating environmentally friendly blocks, let's delve into Carmody Groarke's journey. They collaborated with a group of experts in materials, legal professionals, and authorities to design the Gent Waste Brick. This brick was specifically crafted to be used on the exterior of a fresh wing constructed for the Design Museum Gent in Belgium.
Made from 63% recycled waste from the local city and utilizing hydraulic lime instead of cement as the main adhesive, these bricks undergo curing instead of the traditional firing process, and gain their strength through carbonation with atmospheric carbon dioxide.
As a result, this leads to a brick that has only one-third of the carbon emissions compared to a typical clay brick from Belgium if measured over a span of 60 years (with 0.17kg CO2e/kg for our brick compared to 0.54kg CO2e/kg for the clay brick). By using our brick instead of clay brick, a total of 107 tonnes of CO2 emissions can be saved during the construction of the extension.
Using a highly localized and easily reproducible method, bricks are manufactured on a previously unused plot of land in Gent without producing any emissions, by-products, or waste.
The certification process includes assessment based on European standards and collaboration with the Belgian Construction Certification Association, the authoritative body for certifying construction practices.
The blog section could be rewritten as: Funding for the project was obtained from Circular Flanders, a government-supported organization in Belgium, as well as from developer Sogent. According to architect Sian Ricketts from Carmody Groarke, the project offers valuable insights that can be applied to similar work in the UK. Ricketts explains, "What impressed us the most was how easily accessible their waste streams are, compared to those in the UK. In order to replicate their approach, we need to enhance the accessibility of our waste streams and waste systems. This requires establishing a set of principles and a methodology."
In an effort to push forward with innovation, the architect is collaborating with PhD students from Imperial College London as part of the Design Museum's Future Observatory research program. Together, they are exploring the potential of incorporating the principles of utilizing excavated waste in bricks, along with the ongoing development of cement alternatives.
According to Ricketts, lime contains embodied carbon due to the firing of limestone. Therefore, it would be fascinating to explore the use of alternative binders to reduce the amount of energy involved in the process.
Are you ready for something new appearing on the nearest wall?
Sugarcrete, a groundbreaking creation by the University of East London in collaboration with Tate & Lyle Sugars, has been selected as a contender for the esteemed Earthshot Prize. This innovative material serves as an eco-friendly substitute for traditional bricks, utilizing by-products from sugarcane. Architect Grimshaw recently revealed its initial practical use through the introduction of a prototype slab.
Scientists at the University of Colorado in Boulder, United States, have engineered a remarkable brick that possesses the ability to actively absorb carbon dioxide (CO2) from the air, essentially making it a "living" brick. This revolutionary development offers the possibility of producing bricks that not only have a positive impact on reducing carbon emissions but also presents the potential for enhanced self-repairing construction materials.
I would like to express my gratitude to the Footprint+ Conference for facilitating the gathering of these businesses.